| Studies on Testing of Surface-Treated Plywood. II. Adhesive Strength of Coat Film to Base of Printed and Pre-Finished Plywoods by Peeling Test Shinji Hirai, Yoji Kikata, Hiroyuki Honda : Mokuzai Gakkaishi 9(3), 102-106 (1963) [Original Article]
The authors experimented and studied a peeling test of coat film of printed and finished plywoods. Applying a part of veneer (Betula Maximowiziana REGEL) on the finished surface of plywood with an epoxy resin adhesive for a width of 10 cm, the plywood was slit 1 cm wide through the veneer and coat. Gripping the free edge, the veneer strip was peeled with the coat film from the plywood at 15°, 20°, 25°, 30°, 35° angles (α), and the peeling force (P) was measured (Fig. 1). Both the perpendicular component of the force Psinα and the moment effect P1/2sinα/2 vary lineally in relation to a respectively, so these are indicated by the following form: Psinα + aP1/2sinα/2 = b (1) here, a and b are constants. On the other hand, regarding the veneer strip on the plywood as the elastic beam on the, elastic floor, the following formula is derived from the elastic equation: σt = (4k/EI)1/4Psinα + 2k1/2P1/2sinα/2 (2) here, σt is adhesive strength of veneer strip with coat to plywood, E is YOUNG's modulus of strip, I is moment of inertia of strip and k is a constant. Putting eq. (1) and (2) equivalent, k = a4/4EI, σt = (4k/EI)1/4 · b = ab/(EI )1/2. Thus the adhesive strength is calculated from experimental results, and these are shown in Table 2. Table 1 indicates the results on the veneer-overlaid plywood by the same method.
|
|
| Puncture Test in Plywood and Hardboard. II. Shitomo Mamada : Mokuzai Gakkaishi 9(6), 203-207 (1963) [Original Article]
To obtain the breaking load, deflection and absorbed energy in puncture test, plywood and hardboards were supported in circular plate of 20cm diameter. A striking block, the weight of which was 1kg and the radius of point circle was 2.5cm, was equipped with an accelerometer as illustrated in Fig. 1, and the relations of acceleration g (load)-time t(deflection) were taken out by oscilographs (Fig. 3) in Braun tube. Fig. 2 shows experimental opparatus to obtain oscilographs. Static tests by the similar system were also carried out to obtain static load and deflection. The physical properties of test boards are shown in Table. 1. As for the three formulae 4,6 and 7 to calculate the puncture deflection, formula 6 was considered to be most applicable. The values of deflection obtained from respective formula are shown in Table2. The test boards were supported in three conditions, they were : "simply supported", "loosely clamped" in which boards were clamped by hand, and clamped in which boards were fixed as tightly as possible by pincers. Examples of obtained oscilograph are illustrated in Fig. 3, in which the first maximum points of curves show the breaking point of test boards. Table 3 shows examples of g and t obtained at the breaking. The relations between impact and static test are shown in Table 4. The breaking load and deflection, and absorbed energy to break are shown in Table 5.
|
|
| Puncture Test in Plywood and Hardboard. III. Shitomo Mamada : Mokuzai Gakkaishi 9(6), 208-210 (1963) [Original Article]
The apparatus, method and specimen in study were the same as shown in the previous report. This experiment was conducted to study the influence of some factors on the breaking load, deflection and absorbed energy in puncture test. The obtained results were as follows : 1) As shown in Figs. 1 - 4, in general, the breaking load decreases slowly; on the other hand deflection and absorbed energy increase as the impact velocity increases. 2) As for the 5cm radius of point circle of striking block, the oscilograph, as illustrated in Fig 5, indicates an abnormal curve. The results for 1cm radius are shown in Fig. 6. 3) As shown in Fig. 7, the breaking load and deflection, and absorbed energy to break increase as the weight of striking block increases.
|
|
| Panel and Plate Shear Test of Plywood Isami Takami : Mokuzai Gakkaishi 10(1), 1-9 (1964) [Original Article]
Incorporated in this report are the results of panel and plate shear test on lauan plywood (3 types A, B, C) panels that did not buckle in test. Each panel was made from 5 plies of a lauan veneer and the angle between the edge of panel and direction of face grain is at 0° and 45°(Table1 1). It was known that the shear modulus of elasticity measured by plate or panel (B-method) shear test is nearly equivalent in comparison with that mathematically calculated from VOIGT'S theoretical investigation in use of the several YOUNG's modulus of bending or tension, as bending corresponds to plate shear and tension to panel shear, in the same plywood (Table 5, 6). The value of shear modulus measured by panel shear test (B-method) was quiet equal in the case of both normal and inverse shear, and more correct than the value in A-method, because in the calculated bending deflection on the box-beam with plywood web using of the shear modulus measured by B-method, the theoretical (calculative) value is all the same as the experimental (measured) one (Table 7).
|
|
| Creep Deformation in the Pressing Process of Plywood Motoaki Okuma : Mokuzai Gakkaishi 10(1), 17-21 (1964) [Original Article]
Heating platens were set to the heads of a creep testing machine, and during the pressing of veneers with or without adhesive at different temperatures, the total thickness was measured. The author applied the experimental results to an equation δ = A logt + B (1), where δ : compressive deformation during pressing (cm), t : pressing time(min) and A, B : experimental constants. The results obtained are summarized as follows : 1) The compressive deformation is found to be larger with the increase of moisture content (especially the amount of the water contained in adhesive), the temperature of the platen, the pressure and the pressing time (Figs 3,7). 2) The resultant decrease of total thickness of the plywood during bonding ( = initial total thickness of veneers minus final thickness of plywood) has a linear relation to the pressure, and it's recovery is very small (Fig 6). 3) In the case of bonding 5-ply plywood, creep deformation curve is divided into three parts on the δ - logt relation, and this tendency becomes more conspicuous as the moisture content of plywood increases (Fig. 7).
|
|
| Studies on the Powdered Dry-bonding Process in the Manufacture of Plywood. I. On the Relation between the Gluing Condition and the Strength of Adhesion Tsutomu Tanaka : Mokuzai Gakkaishi 10(4), 131-135 (1964) [Original Article]
Powdered Urea Resin is commonly used after dissolving in water and adding a hardening agent ; but in this study investigation was made about the dry-bonding process of powdered urea resin adhesive with a hardening agent previously mixed. The following results were obtained by consideration of the relation between the condition and the strength of adhesion in the method in which powdered urea resin itself was spread on the surface of the veneers without addition of water and was hot-pressed. It was newly found not only that good adhesive strength was obtained under the usual condition used in the solution type urea resin, but that this method had the noteworthy features of small amounts of glue spread, low gluing pressure, short pressing time and in high moisture content. It seems that those merits are due to effective utilization of the moisture in veneer and resin in the glue layer. It was also found that this method was superior to those of liquid type by the result of in- and out-door exposure tests for 22 months.
|
|
| Studies on the Powdered-Dry Bonding Process in the Manufacture of Plywood. II. On the Influences of Water on the Adhesion Atsuo Tanaka : Mokuzai Gakkaishi 10(5), 188-192 (1964) [Original Article]
The dry powdered urea resin adhesive is not fusible even at 240°C, but it was previously found in the report I that this dry-bonding method can be applied to temperature setting as low as about 40°C. Therefore, in this study the influence of water on the characteristics of urea resin and the strength of adhesion were investigated. By this method a good strength of adhesion was obtained over a wide range of moisture contents 5∼25% in veneers, and even with still higher contents the failure of adhesion by the puncture of veneers was removed merely by using much bigger amount of glue spread. It was found that urea resin was not fused by heat but dissolved in water contained in wood, and as this result the wettability to wood was obtained. Having in mind the ratio of total water to urea resin in the glue layer, it seems that the mechanism of adhesion in this method is not essentially different from that of the liquid type, and the excellent features discussed in the report I are due to the low water ratio.
|
|
| Studies on the Discoloration of Wood III. Acid Stain Katsumi Takenami : Mokuzai Gakkaishi 11(2), 41-46 (1965) [Original Article]
Acid stain is a trouble frequently found in decorative plywood manufacture. In this paper, studies were carried out on (1) the relation between pH and acid stain with oxalic as well as hydrochloric acid, (2) influences of light and (3) stain-sensibility of 19 different woods. Specimens of sliced veneer soaked in acid solutions of various pH were exposed to light in different ways such as under mercury lamp, indirect sunlight in experimental room, or put in a dark place. Color difference (NBS unit) of the treated specimens were were measured by HUNTER color and color difference meter; furthermore, spectral reflectances of 19 different woods were measured by spectrophotometer to calculate their trichromatic coefficients. Results obtained are as follows: 1) In acid stain, color development is, first, rather strong, but gradually fades away presumably due to photochemical reaction (Fig. 1). As coloration is almost the same in nitrogen atmosphere as in air, it appears that oxidation by air does not have a direct relation with acid stain (Table 1). 2) Acid stain remarkably increases below pH 1.5∼2 but is very weak at pH 2∼5 as seen in Fig. 3. 3) Colorations were all pale red, similar to each other, and could be divided into three groups: strong, medium, and weak, as shown in Table 2 by visual inspection. From figures given in the table, any relation between acid stain and tannin content could not be found. 4) Specimens extracted with hot water did not give coloration with acid. This fact would lead to the conclusion that extractives like polyphenols and related substances are responsible for the acid stain.
|
|
| Studies on Water Soluble Phenol, Resin Adhesive for Plywood Yuzo Nakarai, Toshiki Watanabe : Mokuzai Gakkaishi 11(4), 137-141 (1965) [Original Article]
In this study we experimented on the improvement of adhesion properties for water soluble phenol resin adhesive for plywood. The result are as follows. 1) On the condensation reaction of phenol and formaldehyde, if resorcinol is added in the ratio of 5∼10 percent to phenol, it is possible to obtain the perfect water soluble phenol resin adhesive at about pH 7.0, not using much alkali catalyst as usual. 2) When resorcinol resin was mixed in the ratio of 20∼30 parts to 100 parts of water soluble phenol resin adhesive, an adequate shear strength was obtained even when the curing temperature was dropped to 100∼120°C. 3) It is efficient as much as 2) to add the resorcinol and formaldehyde in the ratio of 5∼10 parts to 100 parts of water soluble phenol resin adhesive. In the case of the alkaline phenol resin adhesive, this tendency is especially remarkable.
|
|
| An Electoron Microscopic Investigation on the Gluing of Wood (in English) Hiroshi Harada, Yoshio Okuno : Mokuzai Gakkaishi 11(6), 240-244 (1965) [Original Article]
As one of the structural studies on the gluing of wood, the application of electron microscopy in an examination of the glue line of plywood has been employed. Plywood from Japanese birch (Betula Maximowicziana) was glued with urea- and phenol resin, and urea resin extended with wheat flour. Ultrathin sections of plywood incorporating a glue line were taken from a portion of the plywood, and the interrelationship between the glue and the wood substrate were observed with the aid of electron microscopy. Two types of the interrelationships of veneer and glue line were noted; between excised and unexcised walls. When sections of plywood glued with urea- and phenol resin were examined, it could be seen that the type of surface had no effect on the contact of adhesive, and that within the range of electron microscopic resolution, there was complete contact between the glue and the wood surface. There was a homogeneous appearance to the glue line except when the resin was extended with wheat flour, creating a variegated pattern due to differences in electron density and to the presence of micropores.
|
|
| Puncture Test in Plywood and Hardboard. IV. Shitomo Mamada : Mokuzai Gakkaishi 11(6), 245-247 (1965) [Original Article]
To obtain the load and the absorbed energy at breaking through test in puncture test, plywood and hardboard were supported in circular plate of 20cm diameter. A striking block had a rod at the point which was respectively 10, 15, 20, and 25mm diameter and 12cm long. The buffer board (20mm particle board) was laid on a bed 10cm under the test board (Fig. 1). The oscilographs in this test, which were taken out by the same method as in the previous report, were shown in Fig. 3. In Fig. 2 (a model of oscilograph), the first convex (left, t0) shows the moment of striking at the test board and the second (right, t1) shows the moment of striking at the buffer board after passing through the test board. Assuming that v1 was constant as the test board was close to buffer board, we obtained formula (1). Where s was distance from rest board to buffer board and v1 was velocity after passing through test board. From formula (1) we obtained formula (2). Where, E was absorbed energy for breaking through the test board, t0 was velocity at the moment of striking the test board, and m was mass of striking block. The obtained results were shown in Figs 4, 5, and 6. The comparison between the values in this report and the values in a previous report were shown in Table 2, which indicated that the energy for passing through after breaking was larger in plywood than in hardboard.
|
|
| Determination of Wood Moisture Content by Neutron Scattering Shigeo Onodera, Saburo Sakamoto, Sadao Sawada : Mokuzai Gakkaishi 12(1), 1-5 (1966) [Original Article]
The possibility of a neutron scattering method for measuring wood moisture can better be understood by brief consideration of patient point in the principle. Using this method, wood moisture can be measured more directly and non-destructively compared with a number of other methods. Once the fast neutrons reach thermal energies they come to a thermal equilibrium with the surrounding atoms and no longer lose energy. They now scatter in accordance with the theories of gaseous diffusion until they are captured. From a consideration of the σs and ξ in Table 1 it becomes clear why hydrogen should be more effective than other elements in slowing neutrons. If a counter to detect slow neutrons is placed near a source of fast neutrons in wood, the percentage of counts registered will be a function largely of the amount of hydrogen. But this method has been used unsuccessfully for measuring the quantity of water stored in small amount of materials. We found several new approaches in this test. It is described in this paper that moisture determination of wood chip, veneer, and plywood can be measured with considerably high precision by using fast neutron source (Ra 1 mg + Be), a BF3 counter and moderator (water and a block of paraffin). As the paraffin block used as slowing-down material is presumed to be the effective source of slow neutrons, its arrangement and quantity will have a remarkable influence on the counting rate of neutrons. The present experiments, therefore, are performed with a geometrical arrangement in which the paraffin block is kept as close as possible to the detector and the test sample, because this arrangement is found to be the most excellent. The detectable moisture content in the wood of 4 mm in thick and wood chip is 7 per cent, which is obtained from the experimental results with regard to the standard deviation of the counting rate.
|
|
| Studies on Mechanical Properties of Plywood. I. On Specific Gravity and Shear Strength Motoaki Okuma : Mokuzai Gakkaishi 12(1), 15-20 (1966) [Original Article]
A systematic investigation has been undertaken to provide mechanical data on plywood. The first results of the investigation presented in this report are those of specific gravity and shear strength. Plywood for test was made of rotary cut Bagtikan veneer (thickness 1mm and 2mm, specific gravity 0.585) in our laboratory. Urea resin adhesive was used and press condition was 120°C, 10 kg/cm2, 1 min for 1 mm thickness of plywood. Experimental results are summarized as follows : 1) The specific gravity of plywood has a linear relation with coefficient f (cf. the remark of Table 2). Comparing the experimental formula with the theoretical one, the average thickness of the glue line is calculated to be 0.0218 cm. 2) The shear strength test was made by the JIS method of wood shearing test (Figs. 3 and 4). σs90 + σs0 and σs90 + σs0 [σs90 and σs0 are shear strength (kg/cm2), cf. the remark of Table 2] have also linear relations with f and K0 (Figs. 5 and 6). K0 is the coefficient of plywood construction (cf. the remark of Table 2). These facts lead to formulae by which we can calculate shear strength of plywood from their construction. Then shear strength of veneer (s1, s2) and glue line (sr12) in plywood were calculated (s1, s2, sr12 : cf. the remark of Fig. 7). s1 = 45.2 (kg/cm2), s2 = 93.0 (kg/cm2), sr12 = 445.3 (kg/cm2).
|
|
| Studies on Mechanical Properties of Plywood. II. YOUNG's Modulus in Bending Motoaki Okuma : Mokuzai Gakkaishi 12(1), 20-25 (1966) [Original Article]
The equations (2), (3), (4) are derived from the theory of composite beam, where, E0, E90, E45 : Young's modulus in bending of plywood, when the grain of the face veneer is respectively parallel, perpendicular and 45° to the span. e1, e2, e45 : Young's modulus in bending of veneer, when the grain is respectively parallel, perpendicular and 45° to the span. er12 : Young's modulus in bending of glue line (composite layer) in the specimen, of which the face veneer is parallel or perpendicular to the span. er45 : Young's modulus in bending of glue line (composite layer), of which the face veneer is 45° to the span. tr : Thickness of the composite layer (tr = 0.0218 cm) K1, K2 : Coefficients of plywood construction. They are calculated from the equations (5) and (6). The equations (7), (8) are derived from the equations (2), (3). E0 + E90 and E45 have liner relations with K1 and E0 - E90 has also linear relation with K2. So the author carried out bending tests on plywoods which were prepared by the same method as shown in the first report. The results are shown in Table 2 and Figs, 2, 3, 4. And the empirical formulas (9), (10), (11) are derived where the unit of E is 103 kg/cm2. From these experimental results, the formulas (12), (13) are obtained. Comparing equations (2), (3), (4) with (12), (13), (11), Young's moduli of veneer and composite layer (e1, e2, e45, er12, er45) can be also calculated.
|
|
| Studies on the Mechanical Properties of Plywood. III. Rolling Shear Strength and Horizontal Shear Strength Motoaki Okuma : Mokuzai Gakkaishi 12(2), 71-74 (1966) [Original Article]
Four kinds of sample plywoods were prepared with respectively 1, 2, 3 and 4mm veneer as core in the same way as shown in the 1st report. The wood species is Bagtikan (Parashorea malaanoman MERR..) Test pieces are shown in Fig 1. A and B are for the rolling shear test in which the shearing force works perpendicular to fiber direction, and C is for the horizontal shear test in which the shearing force works parallel to fiber direction. The shearing force works to open lathe checks in A and to close them in B. The notches are cut to the center line of the core veneer, and the distance between notches are varied in three stages. Test results are shown in Table 1 and Figs. 2, 3.
|
|
| Studies on the Mechanical Properties of Plywood. IV. Young's Modulus in Tension and Tensile Strength Motoaki Okuma : Mokuzai Gakkaishi 12(2), 75-80 (1966) [Original Article]
Tensile tests of 11 kinds of veneer construction-plywood (shown in 1st report) have been carried out and relations between veneer construction and YOUNG's modulus in tension and tensile strength have been investigated. If we take the construction coefficients of plywood as f and K0, empirical formulae (8), (9), (10) are obtained, from which calculating formulae (10), (11), (12) are derived as to YOUNG's modulus. By similar method, calculating formulae for tensile strength (16), (17), (18) are derived. In this case, f : Number of glue lines in the unit thickness of plywood,  K0 : Coefficient of plywood as to veneer construction. 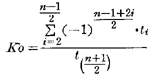 n : No. of plies ti (i = 1,2,…(n - 1)/2) :cf, Fig. 2 Then YOUNG's modulus in tension and tensile strength of veneer and glue line (composite layer) are also calculated.
|
|
| Studies on the Mechanical Properties of Plywood. V. Shearing Modulus in Panel Shear Test Motoaki Okuma : Mokuzai Gakkaishi 12(3), 123-128 (1966) [Original Article]
Panel shear tests (ASTM method and LW-improved method) on 11 kinds of veneer construction plywood (given in 1st report) have been carried out. Test results are shown in Table 1. If we take the coefficient of plywood as f, the calculating formulae for shearing modulus (6), (7), (8) are derived. f : Number of glue lines in the unit thickness of plywood. f = (n - 1)/t where n : Number of plies t : Thickness of plywood On the other hand, the theoretical shearing moduli of plywood are calculated from the rhombic system theory using modulus of elasticity and Poisson's ratio, and they are compared with the experimental values (shown in Table 2 and 3). It is verified that the LW-improved method is better than the ASTM method by comparing α090 with β090 (σ remark of Table 2 and 3). An empirical formula is also obtained for the conversion of values of shearing modulus in both methods as shown in formula (14).
|
|
| Studies on the Powdered-Dry Bonding Process in the Manufacture of Plywood. III. On the Gelation Behaviours of Urea-Resin Adhesive Atsuo Tanaka, Kiyomine Takashima : Mokuzai Gakkaishi 12(6), 272-276 (1966) [Original Article]
When urea-resin adhesive is used for bonding of wood, the heat of wetting for the wood in the spreading and the reaction heat of, urea resin in the curing process have effects on the curing rate of urea-resin in the glue line. Therefore, the actual curing time of urea-resin adhesive in the glue line does not always coincide with the gelation time measured in the test tube in the thermostat. This paper is the first of a series in which the studies of the exothermic behaviours of urea-resin adhesive in the curing process will be presented. This paper outlines the gelation behaviours of urea-resin adhesive after mixing NH4Cl hardner by measuring the variation of pH, viscosity, composition and reactant temperature. The results obtained are as follows; 1) In the presence of ammonium chloride hardner, the pH of urea-resin adhesive drops as time goes on and the gelatinization occurs around the same value of pH. Therefore, the larger the rate of pH descent is, the shorter the gelation time of urea-resin is. 2) As the condensation degree of urea-resin progresses, the effect of an added quantity of ammonium chloride hardner on the gelation time is decreased. It seems that this tendency is based on the formaldehyde quantity produced in the curing process. 3) In the case of addition of ammonium chloride hardner, the rate of cure of the urea-resin adhesive is relatively slow in the initial stage before gelatinigation, but in the following stage a very rapid rate of change of cure commences as the pH come near to a critical stage. Here, the formation of the high molecular weight products and the cross-linking of molecules in three dimensions take place. 4) As will be seen from Fig. 7, the general form of the reactant temperature-time curve in the curing process can be divided into three exothermic stages differing in the rate of change of reactant temperature. It seems that this behaviour is mainly attributable to the rate of change of pH and the curing reaction velocity of the urea-resin.
|
|
| Studies on the Powdered-Dry Bonding Process in the Manufacture of Plywood. IV. On the Exothermic Behaviours in the Initial Reaction of Urea-Formaldehyde and Those of Urea-Resin Adhesives Atsuo Tanaka, Kiyomine Takashima : Mokuzai Gakkaishi 12(6), 277-281 (1966) [Original Article]
In a previous paper we studied the exothermic behaviour of urea-resin adhesive in the curing process after mixing ammonium chloride hardner. The first results of the investigations presented in this report are the exothermic behaviours at the addition and condensation reaction that take place between urea and formaldehyde. The next results of those are the effects of the initial temperature of resins, the solid content and the condensation degree of urea-resin adhesives on the exothermic behaviours. The results obtained are as follows; 1) Both the addition and the condensation reaction at the urea and formaldehyde reaction are exothermic. The reactant temperature is affected by the reaction rate. 2) As the initial temperature of the urea-resin adhesives increases, the period of the second exothermic stage shortens and the increasing ratio of the reactant temperature at the final exothermic stage gets large. 3) The higher the solid content of the urea-resin adhesives is, the larger the increasing ratio mentioned above is. 4) The smaller the condensation degree of the urea-resin adhesives is, the lager the increasing ratio mentioned above is. 5) It seems that the exothermic behaviour of the urea-resin adhesives is affected by the rate of the curing reaction and the total calorific value, but we can not presume the change of the reactant temperature by the gelation time alone.
|
|
| Studies on the Powdered-Dry Bonding Process in the Manufacture of Plywood. V. On the Effects of Hardner and Wood on the Exothermic Behaviour of Urea-Resin Adhesive Atsuo Tanaka, Kiyomine Takashima : Mokuzai Gakkaishi 13(1), 1-6 (1967) [Original Article]
The first results of the investigation presented in this paper are the effects of amount of ammonium chloride hardner and ammonium chloride with ammonia, and sorts of hardner on the exothermic behaviour of urea-resin adhesive in the curing process after mixing hardner. The sorts of hardner are ammonium sulphate, hydrochloric acid, oxalic acid, monochloracetic acid and aniline hydrochloride. The next result of those is the exothermic behaviour in the cases in which urea-resin adhesive is mixed with lauan wood flour. The results obtained are as follows; 1) In the reactant temperature-time curve, the first exothermic stage, the second exothermic stage and the final exothermic stage are found only in the case of ammonium chloride and ammonium sulphate hardner. It seems that this behaviour is affected by the change of the curing reaction rate with the pH change, owing to the ammonium chloride-formaldehyde or the ammonium sulphate-formaldehyde reaction. The reactant temperature of the first exothermic stage is further affected by the heat of dilution or the heat of reaction of additional agent. 2) In contact with wood, the exothermic behaviour is further affected by the heat of wetting for wood. But it seems that the exothermic behaviour in this case is not essentially different from that of urea-resin adhesive itself.
|
|